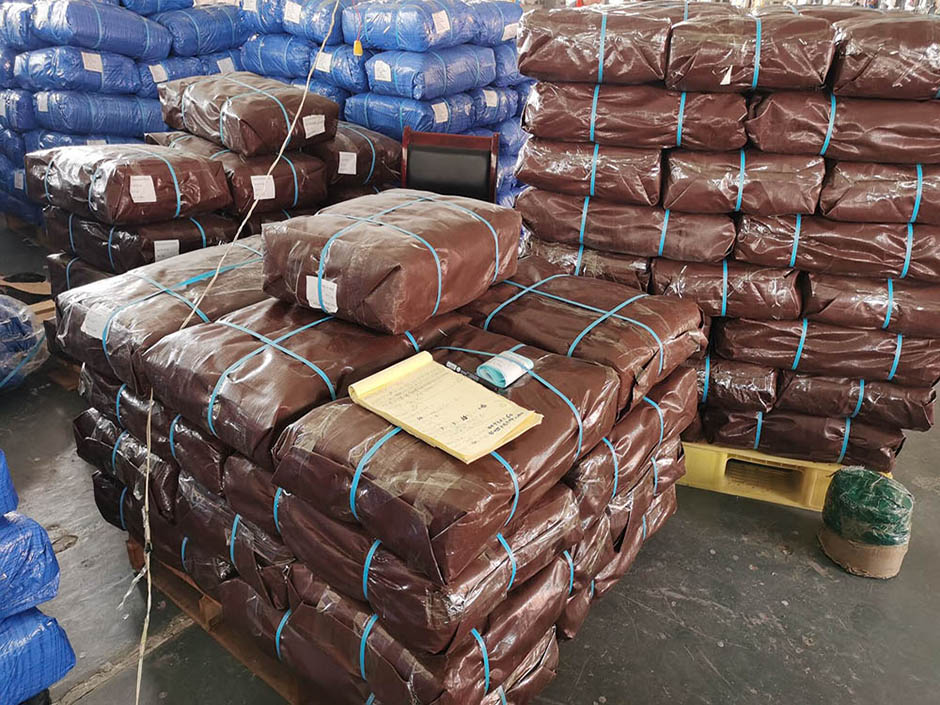
Why is the pre-shipment inspection necessary?
Distributors, Wholesalers, or Retailers with strict requirements for products, will arrange a 3rd party to execute the pre-shipment inspection to scrutinize the supplier's manufacturing process and product quality and ensure the production complies with the governing specification, contract, and purchase order. In another aspect, the 3rd party will examine relative packing requirements like labels, introduction papers, master cartons, etc. Pre-shipment inspection (PSI) can help clients control the risk before the goods are ready to ship.
What are the principles of pre-shipment inspection?
The pre-shipment investigations should follow according to the following principles:
● Non-Discriminatory Procedures.
● Submit the Application 7 days before the inspection.
● Transparent without any illegal bribes from suppliers.
● Confidential Business Information.
● No conflict of interest between inspector and supplier.
● Price verification according to the price range of similar exporting products.
How many steps will be included in the pre-shipment inspection?
There are a few crucial steps that you need to know. They build the whole process to fix any problems before you arrange the balance payment and logistics. These procedures have their specific feature to eliminate the risk of products and manufacturing.
● Order Placement
After the buyer sends the request to the 3rd party and informs the supplier, the supplier can contact the 3rd party via email. The supplier needs to submit the form, including the inspection address, product category & picture, specification, total quantity, inspection service, AQL standard, inspection date, material substances, etc. Within 24-48 hours, the 3rd party will confirm your form and decide to arrange the inspector near your inspection address.
● Quantity Check
When the inspector arrives at the factory, all the cartons contained products will be put together by workers without sealing.
The inspector will make sure that the number of cartons and items is correct and verifies the destination and the integrity of the packages.
● Randomized Sampling
Tarps need a bit large space to check, and it takes much time and energy to fold up. So the inspector will pick a few samples according to ANSI/ASQC Z1.4 (ISO 2859-1). The result will be base on AQL (the Acceptance Quality Limit). For tarps, AQL 4.0 is the most common choice.
● Visual Check
After the inspector requests workers to take the selected samples, the next step is to do a visual check. Regarding the tarps, there are several producing steps: Cutting the fabric roll, sewing large pieces, stitching hems, heat-sealed seams, grommets, logo Printing, and other additional processes. The inspector will walk through the product line to examine all the cutting & sewing machines, (high frequency) heat-sealed machines, and packing machines. Find whether they have potential mechanical damage in the production.
● Product Specification Verification
The inspector will measure all the physical attributes (length, width, height, color, weight, carton specification, markings, and labeling) with the client's request and sealed sample(optional). After that, the inspector will take photos, including the front & backside.
● Functionality Verification
The inspector will refer to the sealed sample and the client’s request to check all the samples, testing all the functions by a professional process. And execute AQL standards during the functionality verification. If there is only one product with severe functional defects, this pre-shipment inspection will be reported as "Disapproved" directly with no mercy.
● Safety Test
Though the safety test of tarp is not a level of medical or electronic products, no toxic substance is still very critical.
The inspector will choose 1-2 fabric samples and leave the consignee address for the lab chemical test. There are a few textile certificates: CE, RoHS, REACH, Oeko-Tex Standard 100, CP65, etc. If the laboratory-grade equipment cannot measure all the toxic substances conditions, the fabric and product can pass these strict certificates.
● Inspection report
When all the inspection processes ended, the inspector will start to write the report, listing the product information and all the passed and failed tests, visual check conditions, and other comments. This report will send to the client and supplier directly in 2-4 business days. Ensure to avoid any conflict before all the products will be shipped or the client arranges the balance payment.
The pre-shipment inspection can significantly reduce the risk.
Besides controlling the product quality and checking the condition of the factory, it is also a way to ensure the lead time. Sometimes the sales do not have enough rights to discuss with the production department, completing their orders in time. So a pre-shipment inspection by 3rd party can push the order to finish quickly than before because of the deadline.
Post time: Feb-23-2022